Programmable logic controllers (PLCs) offer a reliable, versatile solution for controlling and monitoring industrial machinery, allowing you to automate your operations and reduce the risk of errors or accidents. Schneider Electric is a leading manufacturer of PLC hardware, offering a range of models and features to meet the needs of various industrial applications. However, if you’re new to PLC programming, incorporating these devices can seem daunting. That’s why we at PLC Direct will walk you through the key aspects of getting started with Schneider PLC hardware, from choosing the right model to connecting your PLC to other devices. Here’s what you need to know.
Choosing the Right PLC for Your Application
The first step in using Schneider PLC hardware is to choose the right model for your specific needs. Schneider offers several lines of PLCs, including Twido, M238, and M241, each with different specs and features. The Twido line works best for small to medium-size applications, with up to 40 input/output (I/O) points and a compact design that makes it suitable for installation in tight spaces. The M238 and M241 lines offer more I/O points and advanced features, such as Ethernet connectivity, power monitoring, and built-in web servers.
To select the optimal PLC for your application, consider the number of I/O points you’ll need, the type of signals you’ll be controlling (digital or analog), and the required communication protocols. You can consult the specifications sheet and user manual of each model to compare their features and capabilities.
Wiring I/O Modules
Once you purchase your Schneider PLC hardware, the next step is to wire the input/output modules to the device. The I/O modules serve as the interface between the PLC and the external signals you want to control or monitor, such as sensors, actuators, or switches. To wire the I/O modules correctly, follow the wiring diagrams and instructions provided by Schneider. Digital signals are typically connected using screw terminals, while analog signals might require additional calibration and configuration. Ensure that the wiring is secure and insulated to prevent shorts or other electrical hazards. You can also use diagnostic tools to test the signals before adding them to your PLC program.
Connecting Your PLC
The next step in getting started with Schneider PLC hardware is to connect it to other devices and communication networks. Depending on your application, you might need to connect your PLC to a human-machine interface, a supervisory control and data acquisition system, or other devices via Ethernet, serial, or USB ports. You’ll need to configure the network settings, such as the IP address, subnet mask, and gateway, to establish communication between your PLC and other devices. You can then use programming software to set up the protocol and messaging parameters, ensuring that the signals transmit correctly.
It’s essential that you test your communication setup thoroughly, using diagnostic tools or network analyzers to troubleshoot any issues. You can also use security measures such as firewalls or virtual private networks (VPNs) to protect your PLC and data from unauthorized access.
Installing Twido Studio Software
Schneider PLC hardware requires a specialized programming interface, such as Twido Studio, in order to organize and execute your commands. This software provides a graphical user interface for designing ladder diagrams, function blocks, and other PLC programming languages. Simply download the software from the Schneider website and follow the installation instructions. You’ll need to configure some settings, such as the communication port and the device driver, to ensure that the software can communicate with your PLC.
Once you’ve installed the software, create a new project and add the necessary I/O modules and signals. Then you can design your logic program using the drag-and-drop interface, and test it using the simulation mode before downloading it to your PLC.
Implementing Your First Program
Creating a basic program is crucial to familiarizing yourself with ladder logic programming and running a simple output. Ladder logic is a graphical programming language that allows you to represent your control system commands visually. Use the designated Schneider PLC programming software to configure your program based on your needs. Begin by setting up your input and output points, and then write your ladder logic code. You can then download the program to your PLC and start it to test the output signal.
Monitoring I/O Tags
Once you have your first program up and running, it’s time to start monitoring your I/O tags. I/O tags are variables that correspond to the inputs and outputs of your control system. You can use Schneider’s watch window and forcing features to test inputs and outputs as you develop your control program. The watch window enables you to view the values of your input and output tags in real time, while the forcing feature allows you to manually input values to your tags. This can be useful for testing your program under different conditions and scenarios.
Utilizing Additional Debugging Tools
As you work on more complex programs, you may encounter errors and bugs that require more sophisticated debugging tools. Schneider’s PLC programming software provides a variety of debugging aids, including breakpoints, single-step mode, and diagnostic functions. Breakpoints allow you to halt the program execution at a specific point in your code, while single-step mode enables you to execute your program one instruction at a time. Diagnostic functions can help you identify and resolve errors in your code, such as missing or mismatched tags.
Expanding Your System
As your application grows, you may need to add more I/O points, communication cards, and other expansion modules to your Schneider PLC hardware. Schneider offers a wide range of expansion options to accommodate different needs, including analog I/O modules, high-speed counter modules, and Ethernet communication cards. To add a new module, simply plug it into the expansion slot of your PLC and configure it using Schneider’s programming software. Once you’ve added new modules, you can use your programming software to integrate them into your existing control system.
Using Schneider PLC hardware in your facilities can help you optimize your industrial processes and achieve better efficiency and productivity. By following the above steps, you can create a reliable, secure, and user-friendly automation system. But before you can start the implementation process, you need a quality PLC device. PLC Direct stocks a diverse series of Schneider PLCs, allowing you to shop for the perfect model to suit your application and needs. We also carry spare parts, allowing you to repair older models or upgrade your operations as you see fit. Reach out to us today to learn more about the products we have available.
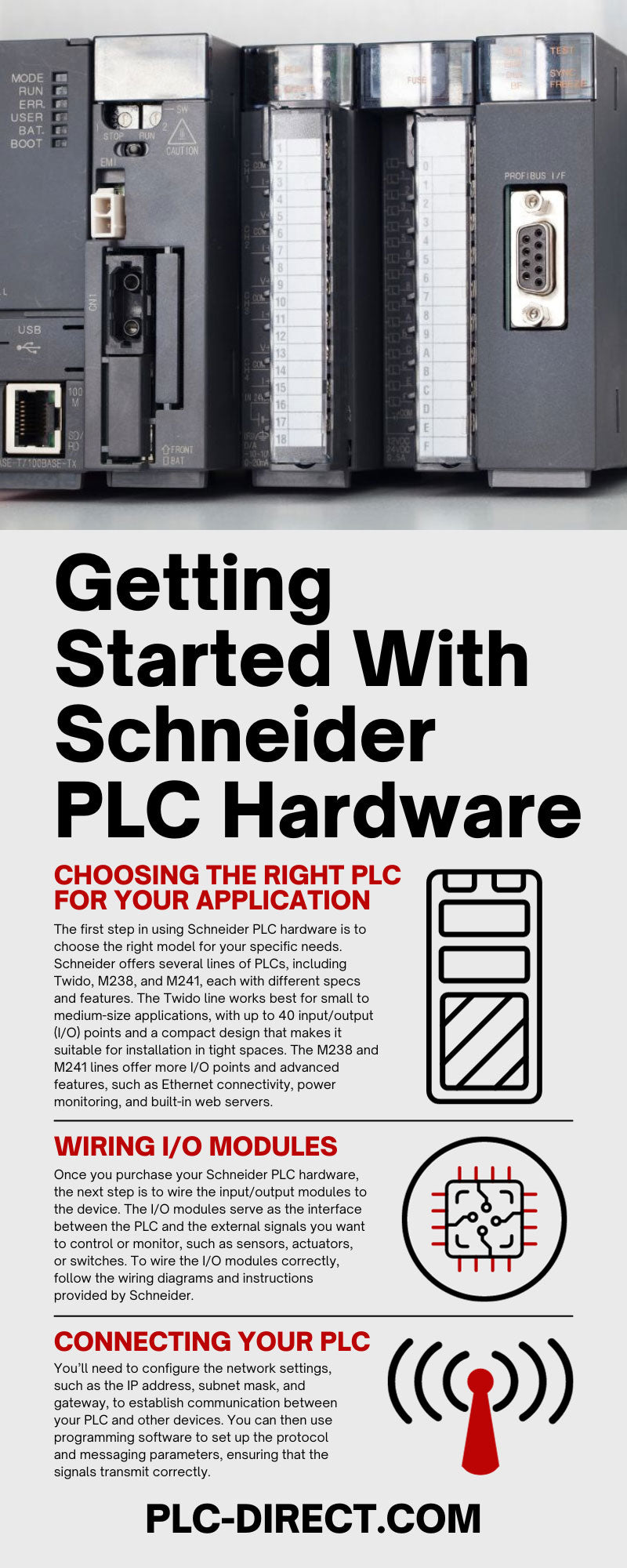